Definition of vacuum infusion standard procedure
The laminate structure (consisting of fibres and core material) is placed dry in a mould coated with a release agent. The tear-off fabric on top and the flow aid are intended to ensure that the resin flows evenly. After attaching the inlet and outlet hoses, the mould is sealed and pressurised using a vacuum pump.
The vacuum draws the liquid resin-hardener mixture into the laminate structure. A resin brake or resin trap prevents excess resin from entering the vacuum pump. Once the laminate is completely filled, the resin supply is stopped. After curing, the component can be demoulded and the tear-off fabric can be disposed of with the flow aid.
Why you lose a lot with standards
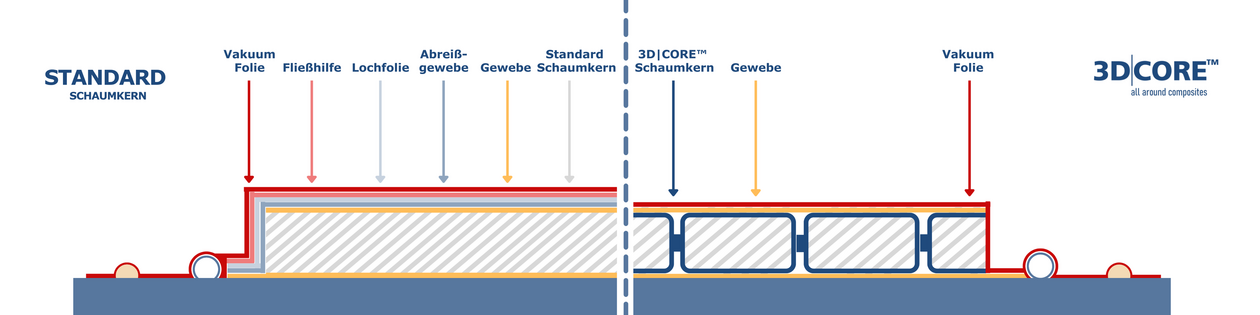
Disadvantages of the standard process
- Average mechanical and technical features
- Technically complex production loops
Material
- High demand for material components
- Additional auxiliaries required
- Additional resin also required
- Deaeration foils and peel ply necessary
Process
- Resin infusion not guaranteed (air pockets)
- Slow infusion process
- Difficult to build up as the core material is less flexible
Outcome
- High component weight
- Increased scrap
Manufacturing costs
- Increased personnel requirements
- Increased work effort
- Increased component costs (time and material)
- Uncertified components cannot be placed on the market in the public legal sense
Benefits of the 3D|CORE system
- Predictable excellent mechanical and technical properties
- Substitutes solid materials (monolithic)
- A patented system
Material
- Already contains integrated flow enhancement
- Integrated homogeneously reinforcing honeycomb structure
- 3-dimensional moldability even for complicated convex and concave shapes
Process
- Defined resin flow throughout the material
- Fast infusion process
- Homogeneous infusion
- Easy draping due to the patented core structure
Outcome
- Significant weight saving with the same technical and mechanical requirements
- More lightweight overall component
- Higher grade and quality
Manufacturing costs
- Less work involved in setting up
- Less personnel required for purchasing and preparation
- DNV certification already available
- Certification for fire protection applications in accordance with EN 45545-2 HL3 also already available
- Lighter overall component
For personal advice call: +49 5221 936393
More about vacuum infusion with the 3D|Core System
We will be happy to answer any detailed questions you may have about data collection, special production processes or individual customization options. Contact us to discuss your specific requirements.
- Acrylic resin
- Epoxy resin
- polyester resins
- Polyurethane resin
- Polyamide resin
- melamine resin
- phenolic resin
- vinyl ester resin
- Urea resin
The 3D|CORE system is compatible with all common and well-known resins and adhesives. We are available to answer your questions at any time.